Expert Packaging Machine Repair Services to Improve Equipment Efficiency
Expert Packaging Machine Repair Services to Improve Equipment Efficiency
Blog Article
Expand the Life of Your Packaging Devices With Specialist Repair Work
In today's affordable landscape, the long life and performance of product packaging equipment are vital for maintaining operational excellence. Engaging specialist repair service solutions not only addresses prompt mechanical and electrical problems yet also fosters a culture of routine maintenance that can dramatically boost tools efficiency. With competent service technicians equipped to make use of high-quality parts that align with producer specifications, companies can reduce downtime and decrease operational costs. However, understanding the full extent of advantages and the ideal technique to choosing a repair work service can be pivotal, leading to a more critical financial investment in your machinery. What should business consider next?
Significance of Normal Maintenance
In the realm of product packaging equipment, the significance of normal maintenance can not be overemphasized. Regular upkeep ensures that machinery runs efficiently, lowering the likelihood of unanticipated break downs that can interfere with production timetables. Normal maintenance includes organized evaluations, cleansing, lubrication, and changes that are essential for ideal efficiency.
Moreover, maintenance serves as a positive strategy to determining potential problems prior to they escalate into expensive fixings. By dealing with small damage promptly, companies can prolong the life expectancy of their tools, safeguarding their funding investments. This precautionary method not just minimizes downtime but also enhances overall efficiency.
Furthermore, routine maintenance plays a critical role in ensuring compliance with safety standards and policies. Well-kept machinery is less most likely to posture safety and security threats to drivers, consequently cultivating a more secure working environment. It likewise helps in maintaining product quality, as correctly working devices is essential in adhering to specifications and minimizing issues throughout the packaging process.
Benefits of Specialist Repair Service
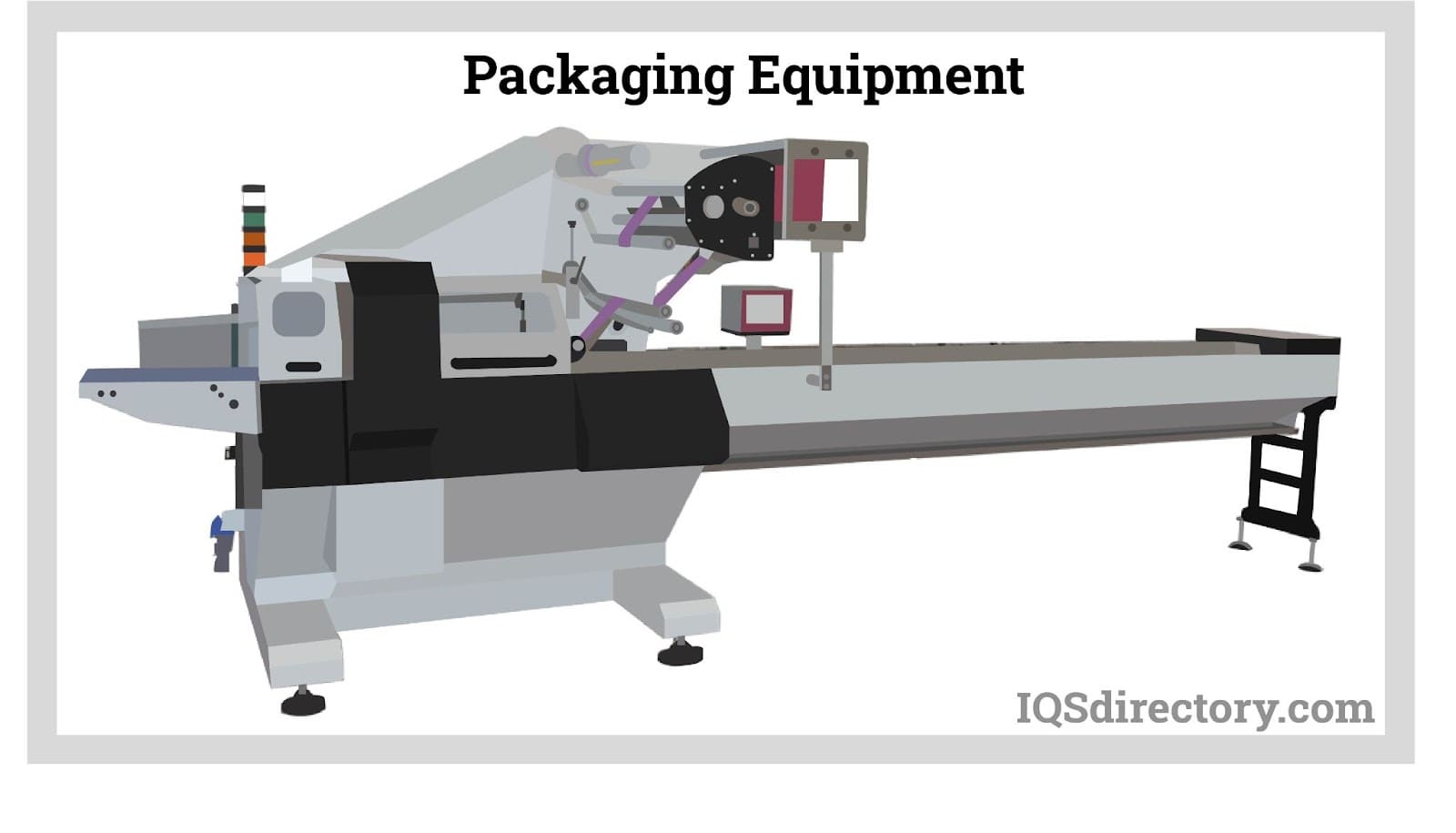
Moreover, professional fixing solutions often utilize top quality parts and products that fulfill or go beyond supplier specs. This commitment to quality makes sure that the fixed tools operates at optimum performance levels, lengthening its life-span and lowering the probability of future malfunctions.
Additionally, specialist repair service can result in price financial savings in time (packaging machine repair). By resolving concerns immediately and efficiently, businesses can stay clear of the high expenses related to total equipment substitutes. Additionally, routine specialist maintenance can maximize the performance of product packaging devices, leading to boosted productivity and, subsequently, higher productivity.
Finally, relying on specialists for repair services promotes compliance with sector requirements and safety policies, mitigating risks related to improper handling of tools. Essentially, investing in expert fixing services not only endures devices capability but additionally adds to an extra reliable, secure, and successful operational setting.
Usual Packaging Equipment Issues
Comprehending usual product packaging equipment problems is crucial for keeping functional performance. Product packaging equipment commonly encounters a series of problems that can disrupt production and compromise item honesty. One widespread issue is mechanical failing, which can originate from damaged components, misalignment, or lack of lubrication. Such failures might lead to unexpected downtime and costly repair work (packaging machine repair).
Another usual concern is electric breakdowns. These can arise from damaged circuitry, blown merges, or out-of-date control systems. Electrical troubles can cause devices to run unpredictably or fail to begin entirely, affecting the whole product packaging line.
In addition, item jams frequently occur due to inappropriate configuration, debris accumulation, or used parts. Jams not only stop production yet might also harm the products being refined, bring about additional losses.
Additionally, inconsistent labeling or securing can develop from equipment wear or wrong calibration, weakening product top quality and conformity with industry criteria. Inadequate upkeep methods often add to a decline in devices performance, making regular evaluations and servicing crucial. By acknowledging and dealing with these typical problems, companies can enhance their packaging procedures and extend the life-span of their equipment.
Picking the Right Repair Service Solution
Selecting the ideal repair service for product packaging equipment is crucial to decreasing downtime and making sure operational efficiency. When reviewing possible service suppliers, consider their know-how and field of expertise in the kind of tools you use. A business with a tried and tested track document in your specific machinery will likely provide even click site more trusted and effective fixings.
Additionally, evaluate the certifications and qualifications of the specialists. Proficient specialists that are fluent in sector standards can identify issues quicker and apply services more efficiently. Researching customer reviews and testimonials can also offer insight into the company's track record and integrity.
An additional crucial aspect is the accessibility of emergency support. Equipment failings can take place suddenly, and having accessibility to a receptive repair solution can considerably lower the impact of downtime. Inquire regarding the guarantee offered on repairs, as this can mirror the confidence the service company has in their work.
Last but not least, think about the communication and assistance structure of the fixing service. A company that focuses on customer support will not only keep you educated throughout the repair work process however will certainly likewise be more probable to use ongoing upkeep suggestions to expand the life of your devices.
Price Cost Savings Via Expert Repairs
How can spending in specialist repair work bring about significant cost financial savings for your packaging equipment? Engaging skilled service technicians for fixings ensures that problems are precisely detected and effectively dealt with, preventing further damage and pricey downtime. Professional repair services use specialized understanding and devices, which can bring about more efficient maintenance than in-house efforts, as a result lowering labor prices.
Moreover, timely repair work can extend the lifespan of your equipment, delaying the requirement for costly replacements. By preserving optimal performance, you additionally boost manufacturing performance, which equates to decrease functional expenses. When equipments run efficiently, there is less waste, and efficiency levels remain high, enabling better earnings margins.
Furthermore, expert repair work commonly include warranties or service warranties, supplying assurance and financial defense versus future failures. This assurance can minimize unanticipated costs and help with better budgeting article source for upkeep.
Last but not least, purchasing professional fixing solutions fosters an aggressive technique to devices management, advertising a culture of regular upkeep checks. This method further boosts general equipment integrity, inevitably causing sustained price financial savings in the future. Prioritizing professional repair work is hence a smart financial choice for companies reliant on packaging tools.
Final Thought

Involving professional repair service solutions not only addresses prompt mechanical and electrical issues yet likewise fosters a culture of routine maintenance that can dramatically enhance devices performance.Expert repair service review of packaging equipment supplies many advantages that can considerably improve operational effectiveness.Just how can spending in specialist fixings lead to significant price savings for your product packaging equipment? Focusing on expert repair work is therefore an intelligent financial choice for services reliant on packaging tools.
In conclusion, the long life and efficiency of product packaging tools can be dramatically enhanced through regular upkeep and professional repair service services.
Report this page